- Minem: el Algarrobo es el primer proyecto en priorizar el recurso hídrico en Perú
- MINEM: Cusco será la primera región del país con proyectos en energía rural trifásica
- Impulso a la equidad de género resaltó en Encuentro de Mujeres Líderes de Ferreycorp
- Inscripciones ampliadas al 24 de abril: Concurso “El Mejor Operador” de Ferreycorp
- PetroTal define inicio definitivo de absorción de Petrolífera Petroleum
Plan de Optimización de Filtros Metso Outotec
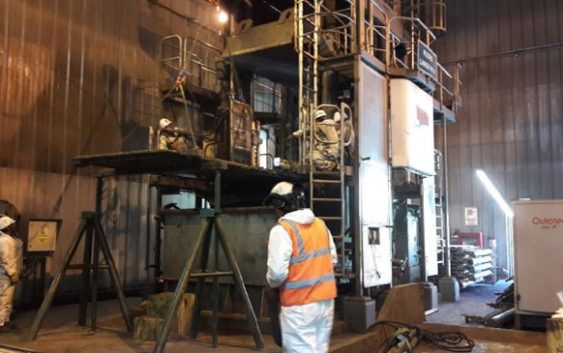
En el competitivo mundo de hoy existe gran presión para conseguir la mayor productividad posible en todos los procesos mineros sin dejar de lado la seguridad operacional.
En Metso Outotec tenemos una estrategia efectiva aplicada a cada uno de nuestros equipos de filtros, cuyo objetivo final es lograr que cada uno de los clientes alcance sus niveles esperados de productividad e implementando programas de mantenimiento de clase mundial que permitan mantener la confiabilidad de la operación.
Hemos desarrollado un plan de optimización de filtros (POF) que nos permite analizar las diferentes áreas funcionales, incrementar la productividad y disminuir costos de mantenimiento y operación de los equipos Outotec Larox® PF 1.6; Outotec Larox® PF 12; Outotec Larox® PF 30; Outotec Larox® PF 48; y Outotec Larox® PF 60.
El plan se soporta en una estructura de 4 fases:
- FASE 1: Assessment (Evaluación)
Inicia con la recopilación de datos históricos de la operación del equipo a través de cuestionarios pre-diseñados acerca de las prácticas de ejecución y planeamiento del mantenimiento, la productividad histórica y sus objetivos a futuro. En esta etapa también se realizan inspecciones “in situ” al equipo en las diferentes disciplinas: mecánica, hidráulica, electrónica, operacional y procesal, y se complementa con el análisis de las características de la pulpa y la auditoría del stock de repuestos críticos. Con toda esta información, nuestro equipo de expertos globales creará el Plan de Optimización estratégico personalizado por Filtro del cliente.
- FASE 2: Entregables
Como resultado del análisis de datos recogidos durante la Fase 1 se desarrolla el Plan de Mantenimiento Optimizado (PMO) basado en los ciclos de trabajo que se registran en el contador de ciclos en cada equipo. Este plan agrupa cinco intervenciones programadas a lo largo de un periodo de tiempo que puede ser variable de acuerdo con las condiciones climáticas, capacidades y tipo de pulpa que procesa cada planta/equipo.
Durante el transcurso de esta fase el cliente recibe entrenamientos denominados “Workshop” que servirán para mejorar el conocimiento de la tecnología, así como revelar las necesidades de entrenamiento al personal de operaciones y de mantenimiento.
3. FASE 3: Acompañamiento
En esta fase se ejecuta la implementación del Plan, para ello el cliente cuenta con diversos soportes que brinda Metso Outotec con garantía de la marca en todos sus procedimientos y ejecución de servicios de mantenimiento, así como los soportes remotos para mantener y/o mejorar la estrategia de operación recomendada. Los Servicios de acompañamiento para las paradas de “Overhaul” (Parada mayor), “Start-Up” (Arranque), Comisionamiento, Modernización y otros tendrán un régimen especial de costos por ser parte del Plan de Optimización de Filtros.
4. FASE 4: Mejora continua
Este programa ofrece una supervisión continua, en ese sentido ofrece al cliente visitas periódicas a planta, libres de costo, para asegurar la correcta implementación y funcionamiento a través del seguimiento, además se recopila data de fallas, paradas no programadas y data de paneles de control para análisis de casusa raíz y prevención de desviaciones futuras en la eficiencia y productividad del equipo, asimismo recomendar mejoras y/o modernizaciones de ser necesario.
Beneficios del Plan de Optimización de Filtros
En primer lugar, tenemos el incremento de la disponibilidad. La máxima disponibilidad para un filtro dentro del plan de optimización es de 90 – 92% dependiendo del número de placas y su tamaño. La diferencia de 10 – 8% con respecto al 100% corresponde al tiempo que necesita el equipo para ejecutar completamente su plan estratégico de mantenimiento.
Otro beneficio importante a considerar será la disminución de paradas no programadas. Se logra debido a que la estructura del plan de mantenimiento cambia las piezas de desgaste en periodos determinados basados en la probabilidad de falla, su criticidad y la experiencia de vida útil de campo recogida a través de la amplia base instalada a nivel mundial. De esta manera proyectamos los cambios y no permitimos que los componentes lleguen a sus periodos de falla, logrando reducir drásticamente las paradas no programadas y con ello el incremento de la confiabilidad del equipo.
En tercer lugar, tenemos el incremento de la vida útil de los componentes. La selección correcta del material de los componentes y las buenas prácticas de operación y mantenimiento contribuyen a mantener todos los sistemas del Filtro funcionando adecuadamente, minimizando el riesgo que aparezcan fallas prematuras, y por ende se amplía la vida útil de los principales componentes de mayor costo de inversión, como las bateas, las parrillas, los sellos de marco, los diafragmas y otros, incrementando hasta en un 30% su vida útil.
Nuestro modelo de trabajo conjunto proveedor-cliente nos permite vislumbrar las necesidades de mejorar las capacidades productivas de los equipos. Estos desarrollos de ingeniería son elaborados por nuestra casa matriz en Finlandia para proveer al cliente de la solución requerida a través de nuestros servicios de modernizaciones.
La optimización de los procesos permite mantener la productividad en el nivel esperado en concordancia con las condiciones de diseño que se utilizaron para determinar la capacidad de producción del equipo (Ton/h), lo que contribuye al aseguramiento de la calidad objetivo del producto final (% humedad del concentrado final).
Por otra parte, el análisis de los datos históricos nos muestra desviaciones de los estándares establecidos y los utilizamos como línea base para la búsqueda de las causas raíz de los problemas antes que se produzcan las fallas. Los resultados nos permitirán modificar y/o actualizar las frecuencias de cambio de los componentes resultando en una mejora continua del plan de mantenimiento.
Parte de los entregables de este plan son: el cronograma bianual de las intervenciones de mantenimiento, actividades generales y listas de repuestos a cambiar en cada uno de los mantenimientos especificados (PM1, PM2…PM5). Esto permite planificar la llegada de los repuestos requeridos antes de la fecha del mantenimiento planificado. Asimismo, permite reducir costos de adquisición por mayores descuentos en compras por paquete.
Finalmente, la consignación de repuestos permite reducir los tiempos de espera (Lead time) a cero, los repuestos están en planta a disposición del cliente, pero en propiedad de . La propiedad cambia cuando el cliente los retira para uso en sus equipos, en ese caso pasan a ser facturados todos los repuestos consumidos en el mes. Permite reducir órdenes de compra a una mensual, disminuye HH (horas hombre) del área logística en solicitudes de cotización. La consignación cuenta con un contrato de precios fijos por un periodo de tiempo a acordar por las partes.
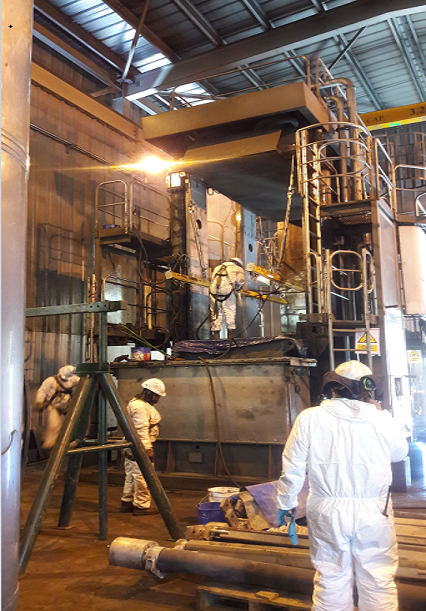
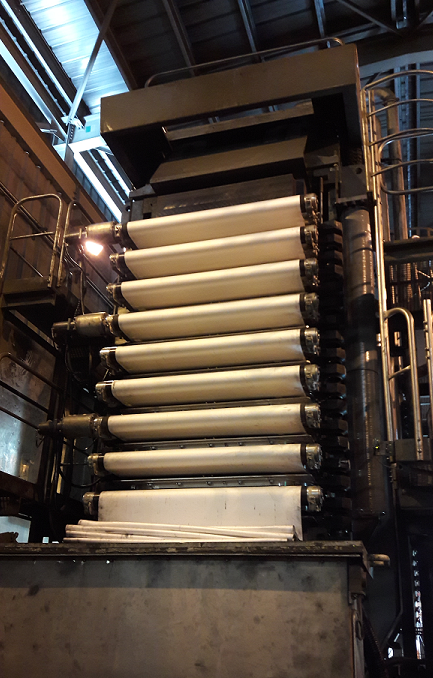
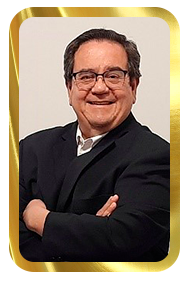